山東模具制造廠家在分型面的選擇上的選擇會影響開模后注塑件是留在動模腔內還是在定模腔內,進而影響注塑件能否成型。那么在選擇注塑模具分型面時要注意什么要點?
Shandong mold manufacturers in the selection of parting surface choice will affect the injection parts after opening the mold is left in the moving mold cavity or in the fixed mold cavity, and then affect the injection parts can be formed. So in the choice of injection mold parting surface should pay attention to what points?
脫模成功影響模具型腔的可加工性,分型面是否會出現“飛邊”或分型面的痕跡是否會影響注塑件的尺寸、形狀、壁厚、模具結構、模具排氣和薄膜模具。因此,在選擇分型面時,要綜合考慮各種影響因素、條件和要求,合理選擇分型面。
The success of demoulding affects the machinability of the mold cavity, whether the parting surface will appear “flying edge” or the mark of the parting surface will affect the size, shape, wall thickness, mold structure, mold exhaust and film mold of the injection parts. Therefore, in the selection of parting surface, it is necessary to consider all kinds of influencing factors, conditions and requirements, reasonable selection of parting surface.
一般情況下,注塑件應留在動模腔內,這樣更便于注塑件的脫模;應避免“障礙體”的阻礙,避免運動干擾,以利于注塑件的脫模和模腔的加工;應設置在不顯眼且易于去除飛邊、毛刺和易于加工的位置;應設置在圓弧R的切點以外的位置,無凹陷和圓弧。
In general, the injection parts should be left in the moving mold cavity, so that it is more convenient for the demoulding of injection parts; Should avoid the obstruction of “obstacle body”, avoid movement interference, in order to facilitate the demoulding of injection parts and mold cavity processing; Should be set in unobtrusive and easy to remove flaking, burr and easy to process position; It should be set outside the tangent point of arc R, without sag and arc.
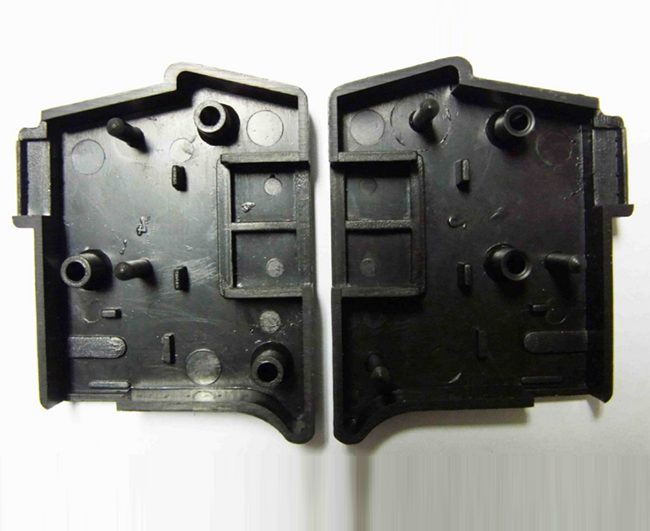
應考慮澆口位置及其形狀的設置;有利于澆注系統和排氣系統的布置;不影響注塑件的尺寸和精度;應考慮塑料的性能和填充條件;應考慮成型的加工性和效率;模具結構簡單,使用方便,可靠。
The location and shape of the gate should be considered; Conducive to the layout of gating system and exhaust system; Does not affect the size and precision of injection parts; The properties and filling conditions of plastics should be considered; The processability and efficiency of molding should be considered; The mold structure is simple, easy to use, reliable.
由于分型面受塑件在模具中的成型位置、澆注系統的設計、塑件的結構可制造性和精度、鑲件的位置和形狀以及成型方法等多種因素的影響。頂出、模具的制造、排氣、操作工藝等因素,因此在選擇分型面時,應進行綜合分析比較,從幾種方案中選擇更合理的方案。
Because the parting surface is affected by the molding position of the plastic parts in the mold, the design of the pouring system, the manufacturability and precision of the structure of the plastic parts, the position and shape of the insert and the molding method and other factors. Ejecting, mold manufacturing, exhaust, operation process and other factors, so in the selection of parting surface, should be a comprehensive analysis and comparison, from several programs to choose a more reasonable program.
Therefore, the explanation of this problem is over, if you have other questions to understand, welcome to our website xunda-china.com consultation, customer service will be detailed answers for you.